Backstory: Aluula
The contemporary ALUULA materials have, over the past few years, become a keyword for premium level wing gear, with it often being utilized within a brand’s top tier wing range. And for good reason – its lightweight and durable properties are catnip for performance wing riders, and it’s helped put many on podiums since its inception. To get some background on this increasingly visible materials brand, we spoke with ALUULA’s Dave Westwood, Director of Sales and Marketing.
Hi Dave. Please start us off from the beginning… How did ALUULA originate and what initially inspired its development?
In 2017, Richard Myerscough, Founder of ALUULA and Ocean Rodeo, saw an opportunity to develop a new fabric that would supersede everything else on the market. At the time there wasn’t a lot of change in the materials being used. Everyone was using Dacron, PU bladder materials and polyester canopy materials. ALUULA was born from a vision to create a new leading-edge fabric that was lighter and stronger than anything else.
The original inventors of ALUULA started playing around with the idea, and there was lots of trial and error. The fabric went through several iterations until it got to the fabric that you see on the beach today. Others have tried to come up with competing fabric, but no one has yet.
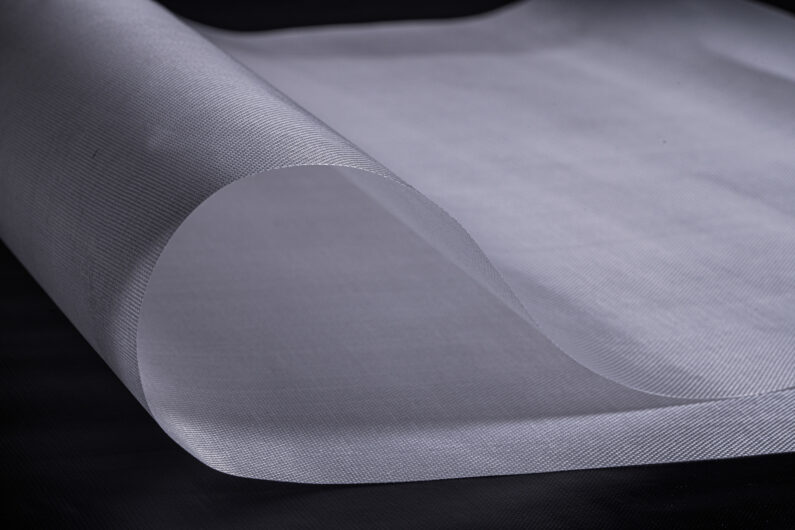
For those who may have heard of ALUULA but are unaware of its relevance in the strong/ ultra-lightweight materials market, please give us an overview in layman’s terms of the materials you produce and how they're utilized in the wingfoil market today.
In simple terms, we make ultra-light high-performance composite textiles that are used in the airframe and leading edge of wings and kites. All our materials contain ultra high molecular weight polyethylene (UHMWPE) in some shape or form.
ALUULA Gold™ is our iconic tried and tested ALUULA fabric, designed specifically for wind sports. We created a fabric with a high modulus outer film and fused it to our ultra-strong ALUULA Core™ to make ALUULA Gold™.
ALUULA Aeris™ is one of our newer lines of composite textile, and we are seeing more and more brands in wind sports start to use it. Unlike Gold™, Aeris™ is a mono-material made from 100% polyethylene, so no glues or adhesives are used in the construction of this textile. We use UHMWPE which enables us to reduce the weight and increase the strength of our fabric. Aeris™ is recycle-ready, and we are working on a circularity proof of concept at the moment.
All ALUULA fabric is ultra-light, stiff and has a high UV resistance. From a wing design perspective, it’s perfect because it allows for a stiff airframe, enhancing performance and responsiveness, it enables a wider wind range, and the lightweight nature of the fabric allows for better handling and better drifting.
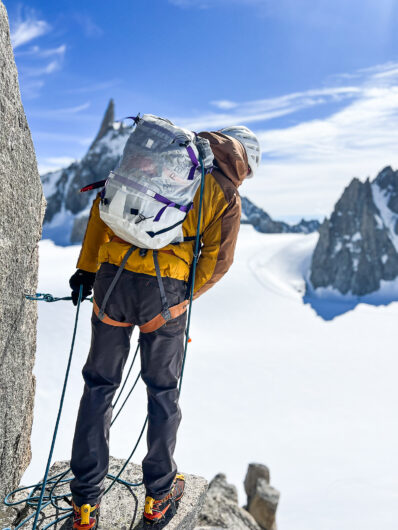
So other than Richard, who were the key players in bringing ALUULA into existence and then to market? And are they still involved in the company today?
Richard and then Pete Berrang, who was brought on to develop the fabric, were the pioneers of ALUULA. Ross Harrington, our Windsports Design Lead was the one designing the kites and wings and putting the fabric to the real test out on the water. After the reverse takeover of Ocean Rodeo, both Richard and Pete became members of the ALUULA board, and Ross is still at ALUULA using his years of expertise to help our customers get the most out of our fabric in their designs.
Did they have a “eureka” moment when they realized they had something that was markedly different to other materials on the market?
We started in kites, testing them in turbulent and gusty air. We realized that ALUULA kites would sit motionless rather than dropping as the balance point had moved aft, and that because the kite was lighter, you could launch it in lighter winds; the wind range on ALUULA kites was impressive. The added rigidity of the airframe meant you could go out in higher wind, sticking on a 10m rather than dropping to an 8m. Everything started clicking into place and that’s when things got exciting… We saw the impact that this could have on leading edge fabric technology and were doing something that allowed us to take kites to the next generation. ALUULA’s success relied on us being able to share it with the whole industry. The proof was in the records set, if you look at kiteboarders like Giel Vlugt, he did the first double loop on an ALUULA kite. When winging exploded, ALUULA proved to be a great match for the airframe because of its performance attributes.
To utilize ALUULA in wings requires different types of stitching techniques right, how have brands adapted to this?
They have adapted well. We provide guidelines to brands and their factories with approved seam or stitching techniques they can follow. These are only guidelines, and they can choose whether to follow or not. Some brands have taken it a step further and evolved their own seam construction based on the load capabilities of our guideline seams.
So what sets ALUULA’s materials apart from other advanced fabric technologies on the market?
ALUULA fabric is unrivalled in terms of lightweight and stiffness. The responsive stiffness of the materials allows for a higher canopy tension which in turn increases performance and wind range capabilities.
Then you look at fabrics like Aeris™ which is 100% recyclable due to its monopolymer construction. With ALUULA, the opportunities for no-sew construction and welded seams are there. ALUULA fabric can be welded to itself, and the seam created is as strong if not stronger than the fabric itself. With our support, some of our customers are starting to test this technology.
Could you tell us a little more about your approach to sustainability and environmental considerations in the materials and processes?
We are focusing on being leaders in achieving circularity in the synthetic material space. As mentioned, our mono-material products are currently recycle-ready and this year we will be pushing to prove the circularity of our materials with various recycling methods.
Alongside this, to augment the use of fossil-derived raw materials, we are actively exploring avenues to utilize bio-based inputs when pristine raw materials are required. Our aim is to realize different ways to reuse and recycle wastage and the end-of-life of products that use ALUULA materials.
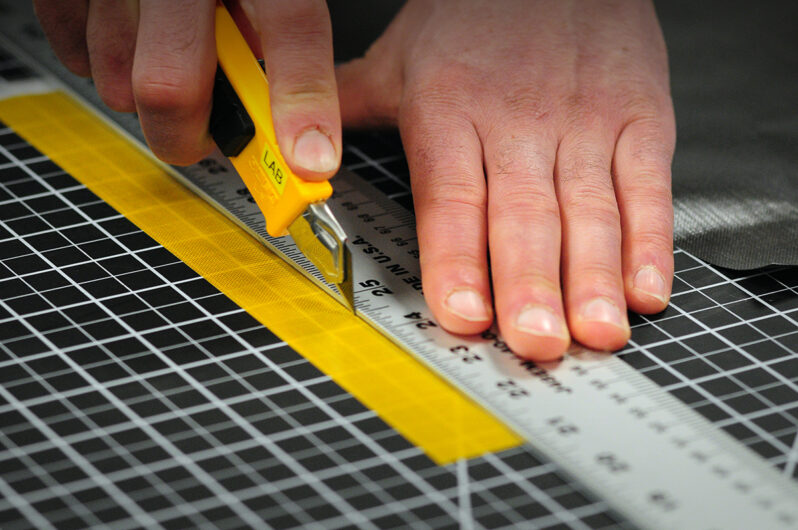
ALUULA disrupted the wind sports market quite successfully, with the material now having been adopted by multiple brands. Was this the intention from the outset?
The intention was to create a fabric that was lighter and stiffer. We didn’t know that ALUULA would work, and we serendipitously instigated a fabric revolution in the industry. The fun really began when we started to share ALUULA with the wider industry because we moved from a position where we were trying to keep our designs secret, to one where we could share our knowledge and learning, and help other designers get the most out of the ALUULA fabric. Whilst it may not have been the intention at the start, we are proud to be working with the leading brands in the industry now.
And other than wind sports, is ALUULA making an impact in any other industries?
The performance outdoor market, so ultra-light packs etc, is one of the fastest growing markets and next year is looking like a big year for that category. The bigger impact in this market will come when companies start creating products that take advantage of the heat-welding and no-sew construction methods that are available with ALUULA. Adapting to this new method takes time, but once companies have adapted, it can reduce the weight of products and increase the seam strength. Our R&D team are always looking out for new innovations, so expect some more exciting news to come later this year.
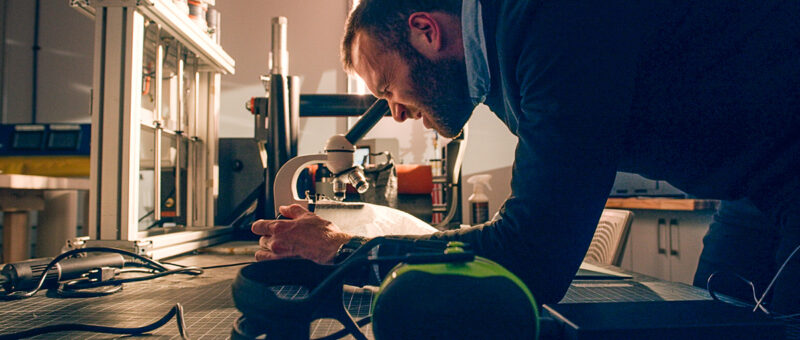
Although it’s still a relatively young company, would you say that ALUULA has evolved significantly since its inception?
Absolutely! The biggest evolution has been the fabric itself, transitioning to 100% polyethylene materials, like Aeris™. We now service a much wider range of industries, which means we are continuously learning more and more about how our fabric performs in different environments. And we are investing more and more in R&D to develop and fine tune our fabric further and accelerate the potential of full circularity.
So how many employees does the company have now, and where are you based?
We are a proud Canadian company based in Victoria, British Columbia and all the manufacturing still takes place on-site. It’s a small but efficient team of around 20 including manufacturing. We’ve brought in some of the best in the business to help us get to the next level, including our new Chief Scientific Officer, Tyler Cuthbert, who has been tasked with pushing the boundaries of what’s possible with our composite textile.
So what more can you tell us as to what’s in store for ALUULA in terms of innovation, applications, and growth?
In the wingfoil sphere, as more people start using Aeris™, we expect to see welded airframes and continuous curve leading edge tubes instead of segmented tubes like they are now. A continuous curve will allow for much better flex dynamics on the leading edge.
More brands are set to launch products in the performance outdoor space, and we are seeing some other exciting innovations in different industries. We have ambitious goals for 2025 and are continuously working with our partners to push the boundaries of what’s possible with ALUULA fabric.
Finally, we’ve always found the name a really intriguing one. Is there any background to it? Or did it just trip off the tongue nicely?!
There is! Ross came up with the name. Alula is the Latin word for ‘winglet’. Alula feathers form a crucial part of the leading edge of a wing, generating lift in momentum. We wanted the name to roll off the tongue a bit more and stand out, so we added the extra U. The feather in the logo represents the lightweight stiffness of the fabric.
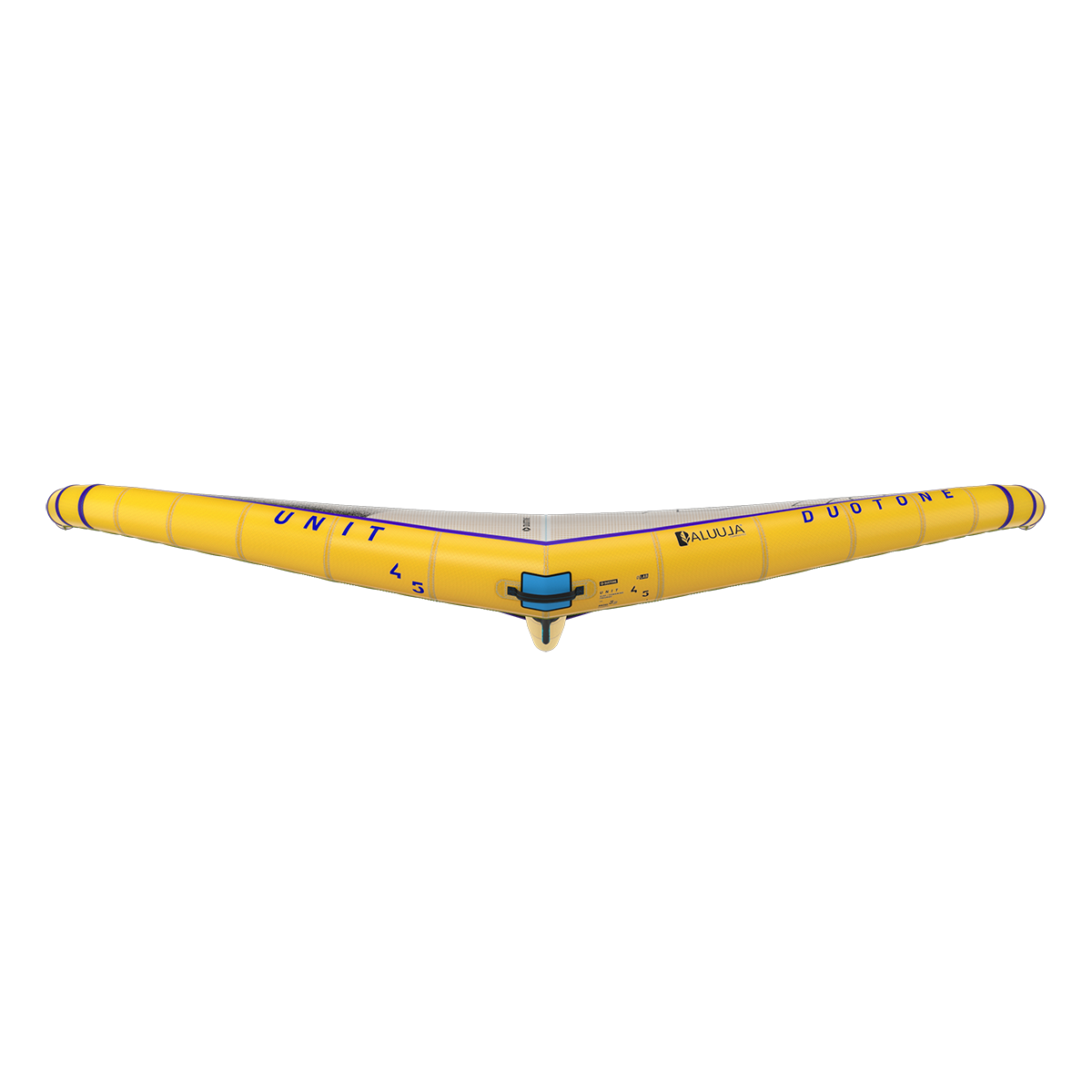