The Innovator: Ultra X
We’re always happy to hear the words “next generation material” as it means we get to don the specs and go down the techy rabbit hole over here at Foiling Magazine HQ. With the arrival of the new Ultra X lightweight laminate, the specs were donned, and we got in touch with the man who was more deeply involved than most, FreeWing’s Design Director, Clinton Filen.
Hi Clinton. Can you start off by giving us a little background to the Ultra X material – how and when did you first come up with the concept?
As a design team working on wings and kites, we have long term ongoing research and development around new materials. We are constantly exploring lightweight laminates, woven materials and blends, looking at new primary materials, secondary materials and/or production processes.
The biggest breakthrough in recent years has been the integration of Ultra PE (UHMWPE) into the materials. These Ultra High Molecular Weight Polyethylene fibers are the lightest and strongest fibers commercially available. This is also known under the trademarks of Dyneema and Spectra.
A lot of work has been done in leading edges and most of this development centers around Ultra PE. Our Hookipa material is a woven Ultra PE and Aluula is a laminated style with an Ultra PE core. For canopies we have been using Ultra PE in our load frame of our kites for around eight years. The canopy is still the most fragile part of the kite or wing and prone to stretch due to its extreme light weight.
The Ultra X is essentially a mini load frame or structural micro grid of Ultra PE. This substantially increases the performance and durability of the canopy. Most importantly it is the same weight as the woven materials (85gsm) of the new generation canopy cloths from our competitors, with far superior strength to weight performance.
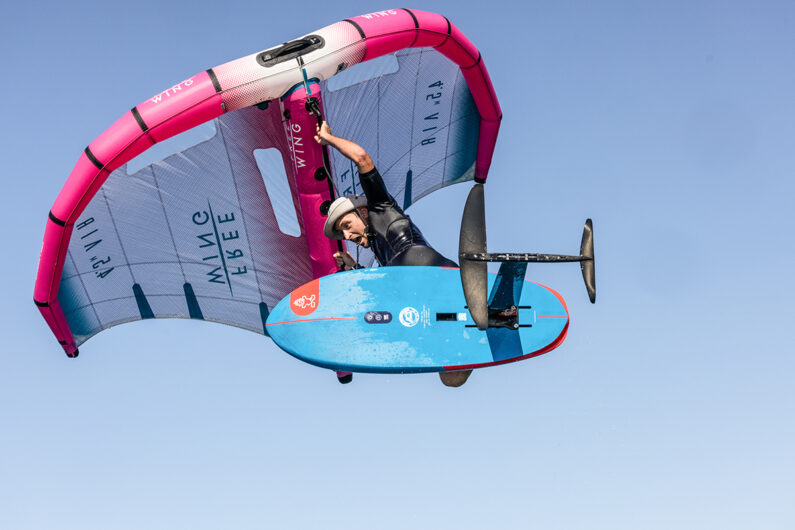
X-ply has been used in windsurfing sails for some time, was it an inspiration for Ultra X and how was the material augmented for wingfoil use?
Yes, I was lucky to be involved in the development of the first generation of ultralight windsurfing rigs some time ago and this is developed to continue these fundamentals. Over the last 10 years the weight of the lightest potential laminates has reduced, we are able to get to half the weight for two films laminated together (traditionally it was around 100gsm). From there you can optimize the balance of weight and durability.
Windsurfing rigs operate under a lot more tension, so you cannot go as light as with a wing. We also needed to consider that the material will get rolled and folded, this is why we opted for a blend of a woven material, Ultra PE grid and lightweight film.
And what are the benefits of this material to both you as a product developer, and to the end user?
As a product developed the material is more stable so it holds its design shape and can handle much more tension. This stability translates into a real benefit to the end user, as the wing will continue to hold its shape for much longer, the Ultra X grid also increases the overall tear strength significantly.
Are there other potential applications for it? Will the material cross over into your kite range for instance?
Currently there are technical limitations to how light we can get the woven component without the price increasing significantly, although many of our kites feature an Ultra PE load frame, which offers similar benefits. We did test this material in kites initially, but kites do not have the same durability challenges as wings. We do share Ultra PE leading edge materials between kite and wing with our Hookipa and Aluula constructions.
How do you go about testing a material like this? How much is in the workshop and how much is “in the field”?
There is a lot of initial lab testing and theoretical development where we will discuss and calculate the weight of various formulations. From there we have a limited run of the materials built and check the lab test data sheets against other fabrics. We build the first prototypes and often need to refine the design to suit the fabric. Then we go into long term field testing in various locations. Each cycle takes around six months plus longer term testing, and every time we change a formulation, we need to go through the cycle again.
“The Ultra X is essentially a mini load frame or structural micro grid of Ultra PE. This substantially increases the performance and durability of the canopy.”
Are there any new considerations in manufacturing when implementing the Ultra X at the factory?
Our factory is very experienced with working in new materials, they will be involved with us continuously during the development and feedback on any new material. The Ultra PE materials are more complicated to work with, very difficult to cut due to the strength of the material, but we are lucky to have an amazing material and production partners.
Manufacture of Ultra PE materials is extremely challenging, as you need to create a very stable material from sensitive raw materials, so there is a constant quality review on every meter of fabric and communication between material supplier, factory and design team.
You’ve used the Ultra X material in the FreeWing AIR Team and the air V4. How’s it gone down with your team riders?
Our Air Team was an immediate hit with our wave and freestyle team as this combines the bombproof Hookipa leading edge with the Ultra X. Essentially a full Ultra PE wing, with slightly flatter shaping for higher wind performance, low drag and light weight. The Air V4 features a fuller canopy for more low-end power and boosting, the combination has been working well with the team.
Does any extra care need to be taken when folding and storing the wings?
It is generally best to roll and fold any high-performance material, instead of “scrunch and bunch”. Leaving the wing flapping in the wind or exposed to extensive UV (sunlight) unnecessarily reduces the lifespan significantly, but this is the same for every fabric.
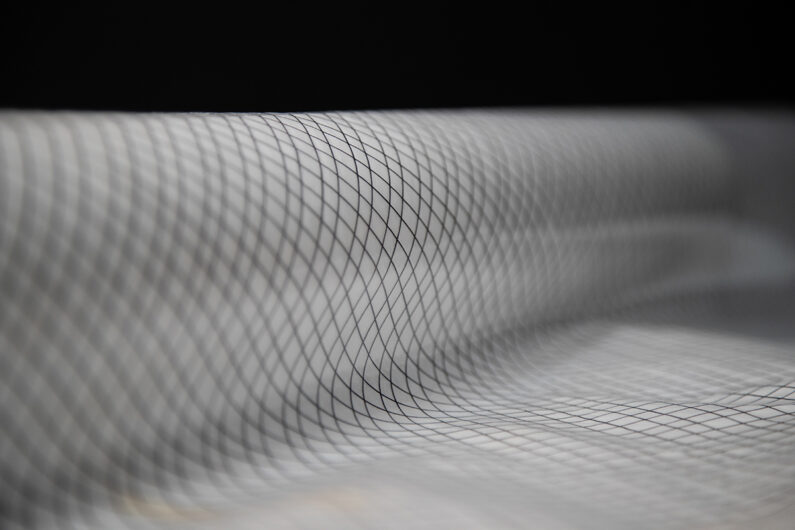
What else is the Ultra X being used in, and can you tell us about anything else that’s coming soon?
The latest of our premium wings are all featuring Ultra X and any upcoming products will see this material continue. We always have some new formulation of material in the works but Ultra X is our newest offering and we are very excited to get more feedback from the market.
“Our Air Team was an immediate hit with our wave and freestyle team as this combines the bombproof Hookipa leading edge with the Ultra X..”
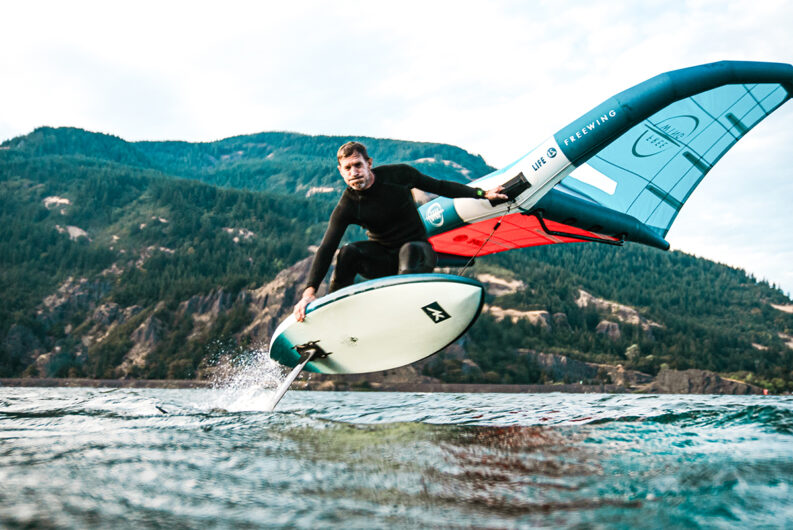